The combination of campus 5G, edge and slicing has transformed the business of steelmaker XISC in China
The impact of 5G is likely to be particularly dramatic in the manufacturing sector, especially for traditional, heavy industries such as steelmaking. The increased automation, productivity and intelligence that 5G can enable will transform manufacturers’ businesses and generate new revenue streams for mobile operators and other stakeholders.
The private 5G network deployed by China Mobile and Huawei for Hunan Valin Xiangtan Iron and Steel (XISC) in China (one of the world’s largest steelmakers) demonstrates the impact that 5G can have. XISC has significantly increased the productivity levels in its plants following the deployment, and is saving USD15 million annually.
Such deployments can also have significant benefits for operators, who will increasingly rely on B2B and private network contracts to drive their revenue growth in the 5G era. The case study analysed in this article highlights both the challenges of meeting large manufacturers’ demanding requirements and the need for a flexible approach to maximise the benefits of 5G for the customer.
The demand for 5G to support digital transformation is high in traditional industries
5G networks enable a far more diverse range of capabilities than previous generations did, and this allows them to support applications and industries that were hitherto unable to use mobile connectivity. This is particularly true for traditional industries such as steelmaking and vehicle manufacturing. Leading companies in these industries have been undergoing digital transformations in recent years, but have been unable to use mobile networks for many mission-critical processes. This has forced them to either use fixed lines for their robots and cranes or to continue to use manual processes, both of which limit effectiveness.
As such, there is a significant pent-up demand for 5G networks that can support a wide range of use cases, including those requiring very low latency or critical responses. The impact of 5G networks can be further increased through integration with complementary technologies such as machine learning and edge compute in order to support highly intelligent decision making in near-real time.
These capabilities led XISC, a company with over 10 000 employees, to implement a 5G solution to address some critical business objectives. These included eliminating information siloes created by a patchwork of different data systems and networks and allowing machines throughout the plant to interoperate and communicate intelligently. Another key objective was the automation of manufacturing and management processes to improve efficiency, yield, product quality and profitability.
Demanding performance requirements and harsh environments make it challenging to deploy and operate 5G networks
Deploying and operating a 5G network in an industrial environment such as a steel plant is extremely demanding and complex.
XISC had automated some of its major production lines, but it needed mobile connectivity and edge compute across its full campus (spanning 5 square kilometres) in order to become ‘fully smart’. This was impeded by the harsh production environment and the presence of various incompatible legacy connections.
XISC also needed to automate a wide variety of processes, each of which had a different requirement for connectivity and data analytics. Some of these requirements were focused on improving process efficiency (such as the remote control of machinery), while others were forward-looking and aimed to improve future efficiency and yield through advanced analytics.
The challenge for operators that are deploying private 5G networks is that each organisation has specific requirements, even within a single sector such as steelmaking. It is clear that one network will not fit all scenarios, yet a mobile operator’s business case is based upon deploying the same network multiple times, rather than building individual networks for each customer.
A flexible platform is essential to enable operators to tailor 5G connectivity and applications to the needs of each customer
The solution to the challenges outlined above is to build a private 5G network that is fully specified and controlled by the customer, but that is based on a broad, flexible 5G and cloud platform. This allows operators to invest in a common set of 5G enablers, thereby enabling them to deliver a customised set of capabilities and applications from common foundations.
China Mobile deployed the private campus network for XISC’s ‘5G Smart Steelmaking Digital Transformation’ project. It tailored the network to the customer’s precise requirements, but based it on a more-generic platform that can be used both to deliver similar customised solutions for other organisations and to meet new requirements at XISC as its business evolves in the future.
The deployment supports three main categories of 5G use cases, which reflect some of the most important capabilities of the 5G B2B platform in general, and which all need to interact with one another. These are:
- process monitoring using drones to generate UHD video streams, supported by augmented reality (this creates massive data upload requirements)
- remote control for machines such as cranes and robots, which requires a very-low-latency response
- machine vision and AI analytics to automate processes such as slab rotation and steel surface inspection.
This combination of use cases requires coverage in every corner of the campus, near-real-time network response and analytics and the capacity to support very large quantities of data. China Mobile deployed a network based on 200 cells in a format that provides the flexibility to assign resources where they are needed, and to improve interference mitigation. This runs in the 2.6GHz and 4.9GHz spectrum bands and supports Super Uplink, with uplink rates of up to 700Mbit/s. Edge computing nodes enable a near-real-time response for latency-critical services such as video streaming, and reduce the end-to-end latency from 26ms to 9.9ms.
The services platform and operations engine that together enable a huge diversity of services to be deployed and modified to suit changing business needs are just as important as the connectivity and edge cloud. Service development and rapid deployment are enabled by a 5G slicing platform called CSMF+. The implementation of CSMF+ has reduced the time taken to provision a new service at XISC from several months to about 1 week.
CSMF+ is part of Huawei’s Network Operations Engine (NOE) layer, which provides three levels of control for use by different departments. NOE.C+ is used by the operator to support the agile launch of services, NOE.N+ enables resource provisioning based on scenarios or network slices and NOE.M+ enables self-service connectivity management for an enterprise IT department. This multi-layered approach supports the flexible sharing of network and service management between the enterprise and the operator, depending on the scenario.
The deployment of a private 5G network using CSMF+ has had a significant impact on XISC’s business. For instance, the low latency and high data rates enabled by the network have improved the reliability of the cranes and robots, which in turn has increased productivity and reduced wastage. Slag addition is an important element of the steelmaking process; remotely controlled robots can add this substance more evenly than humans, thereby creating smoother steel and saving people from having to work in harsh, dusty conditions.
Furthermore, AI analytics can be added to the video streaming and remote control functions, thereby eliminating the need for manual processes such as rotating slabs into the correct position or detecting defects in the surface.
Some of the commercial outcomes highlight the impact that intelligent automation, enabled by top-quality connectivity and AI, can have. XISC says that its detection of steel surface defects has improved from 90% to 95%, leading to improved yield and customer satisfaction. Its output per employee has risen from 920 tons of steel per year to 1380 tons and it has reduced its production costs by 10%. Overall, it attributes a 30% increase in production efficiency to the 5G/edge network, which has resulted in direct economic benefits, including cost savings of CNY100 million (USD15 million) per year.
It is important that additional functions can be built on the platform in the future
Digital transformation is an ongoing process for any large organisation, and it is important that customers such as XISC can continue to build additional services and efficiencies on the same network in the future. This is enabled by a flexible services platform that can take advantage of different combinations of 5G and edge capabilities according to the needs of different applications as they evolve. For example, XISC’s next priorities are to harness 5G to reduce energy consumption even further, while investing in 10 high-priority use cases. These include collaborative design, assisted assembly and full lights-out manufacturing; it will also extend 5G-enabled automation into more aspects of its operations, such as warehousing management.
A flexible, futureproofed network and platform will enable large organisations such as XISC to expand their number of use cases each year and to continue to generate additional commercial benefits, while providing a long-term, high-value customer relationship for the operator (since many of the services and network operations are run on a co-operative basis between the operator and the client). A large, business-critical campus deployment also helps operators to build a body of expertise and vertical industry knowledge that can be applied to other customers. Indeed, China Mobile and Huawei believe that some of the solutions implemented for XISC can be adapted and scaled-up to meet the needs of even larger steelmakers, such as Baowu (the largest steelmaker in China). They can also be modified for other industrial and manufacturing sectors as their requirements for process transformation become increasingly critical in the future.
This article was commissioned by Huawei. Analysys Mason does not endorse any of the vendor’s products or services.
Article (PDF)
DownloadAuthor
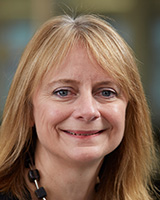
Caroline Gabriel
Partner, expert in network and cloud strategies and architectureRelated items
Survey report
Operators’ requirements for their next-generation RANs: survey results and analysis
Article
Stakeholders must collaborate to prove the security benefits of Open RAN and de-risk early deployments
Forecast report
Mobile packet core: worldwide forecast 2024–2030